Battery technology
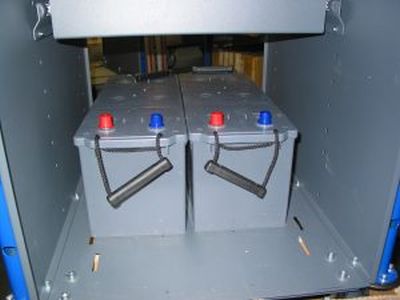
Battery unit and DC/AC converter unit
Securing the power supply is an essential part of mobile workplace solutions. The supply units of the trolley solutions are selected depending on the consumers, especially their supply voltages (AC or DC) and their power consumption (VA).
The supply units of the trolley solutions are dimensioned depending on the power requirements of the consumers and the off-grid working hours. Here the question quickly arises:
Which battery technology should be used?
Below is some basic knowledge and a direct comparison between AGM technology and LiFePo4 batteries. We offer both variants.
The classic. The AGM-VRLA DEEP CYCLE battery. The completely sealed lead-acid batteries are designed in absolutely maintenance-free AGM-VRLA technology for a wide variety of applications.
The batteries are manufactured using the latest technology and are individually tested. Thanks to a special manufacturing process, the battery is extremely resilient and durable. This results in the high cycle stability. The batteries meet the highest standards and are undoubtedly among the most robust and reliable, maintenance-free AGM DEEP CYCLE batteries on the market.
Properties ZL Deep Cycle
- high cycle stability
- maintenance free
- locked
- Leakproof
- long service life very low self-discharge
- Safety valve against overpressure (VRLA technology)
The difference:
The positive electrode is made of (LiFePO4) Lithium Iron Sulfate instead of traditional (LiCoO2) Lithium Cobalt Oxide. The negative electrode consists of graphite (hard carbon) with intercalated lithium. Such an accumulator has a lower energy density compared to the conventional LIFO, but - even in the case of mechanical damage - NOT tends to "thermal runaway."
The difference to conventional lithium-ion cells with lithium-cobalt(III)-oxide (LiCoO2) becomes clear during the charging or discharging process of the LiFePo battery. No oxygen is released in the chemical reaction. Together with lithium-cobalt oxide cathodes, oxygen can lead to a thermal "accident" in lithium-ion accumulators, which under unfavorable conditions leads to the cell igniting on its own.
Due to the solid electrolyte and the cell chemistry, LiFePO4 cells are considered intrinsically safe, i. H. a thermal runaway and membrane melting as with lithium-ion batteries is excluded.
In the following you will find a list of advantages and a comparison between lead gel and LiFePo4 technology
- You only need about 50% of the lead capacity if you want to switch to LiFePo4, which results in over 50% weight and space savings.
- 4 to 5 times the number of charging cycles results in a significantly longer service life.
- A full charge is not absolutely necessary with LFP.
- Very high charging efficiency, almost 100% of the energy fed in can also be used again.
- Even 50Ah LFP can supply 1000W inverters at almost any state of charge.
- High charging and discharging currents possible over the entire state of charge.
- A battery management system (BMS) is mandatory and already integrated
- Flexible end-of-charge voltage, lead chargers can also be used
- Unlike LI-ION batteries, lithium batteries are intrinsically safe - there is no risk of fire
At FORSIS, we see a trend towards LiFePo technology in the future. The benefits are clearly seen above.
Technology lead gel
- Capacity 40Ah, 65Ah, 85Ah or 120Ah
- Voltage 12V / battery
- Number of batteries 2x always connected in series
- Charging cycles approx. 500-600 times to 70% full charge
- Charging current 10A or 15A max.
- max. Discharging Approx. 70% depending on the deep discharge protection
- Design completely closed housing block shape with screw poles
- Weight between 28kg and 70kg depending on the battery
- Dimensions identical
- DC/AC converter 350W, 600W or 1200 W
Technology LiFePo
- Capacity 50Ah / 80 Ah
- Voltage 24V / battery
- Number of batteries 1 piece
- Charging cycles approx. 4000 to 95% full charge
- Charging current depending on the charger max. 1C
- max. Discharging Approx. 98% depending on the deep discharge protection
- Design completely closed housing block shape with screw poles
- Weight approx. 13 kg depending on the battery
- Dimensions identical
- DC/AC converter 350W, 600W or 1200 W
Using a concrete example, we want to work through the dimensioning of a battery supply for a mobile workplace. We assume that the customer wants to configure a large and flexible system and therefore has a large number of end devices
The following printer components should be used on the mobile workstation: FORSIS PANEL PC PROFI S 2150 MT with scanner and various printers: e.g. 2x ZEBRA ZM400, TSC TTP2410MT, HP Laserjet P3015
1. Determination of supply and consumption
Using the manufacturer's technical documentation (data sheet, etc.), the first task is to determine the supply voltage and the power consumption of the devices. To design the battery technology, we have to consider the following two scenarios: Startup and continuous operation
Supply voltage Information on consumption in current consumption or power
A distinction must be made between printing operation or start-up and standby
ZEBRA ZM400 - supply voltage 230V AC / current consumption 5A at 230V AC approx. 1150W n.a.
TSC TTP2410MT - supply voltage 230V AC / power consumption approx. 220 W, no information on current consumption
HP Laserjet P3015 - supply voltage 230V AC / worst case power consumption 750 W, standby mode 10W
PROFI PANEL PC - supply voltage 24V DC / approx. 40W in operation
Scanner - supply voltage 5V DC / power consumption approx. 5W via USB interface of the PANEL PC
Note: The data sheets and manuals often provide relatively flexible information about the maximum values of the devices. An upper tolerance should therefore always be taken into account.
1.1. The start-up of all components at the time of switching on.
Here, all systems start up at the same time and go into operation. The power consumption of the printers in particular must be carefully observed here. The behavior is similar when printing
The customer now tells us, for example, that the TSC printer is used and the following combinations are possible, plus all other consumers such as PCs, etc.
Example: Goods receipt work center:
2x TSC 2x 220W = 440W
PC technology 40W
Total 480W
Example workplace Goods issue:
2x TSC 440W
1x HP 750W
PC technology 40W
Total 1230W
The selection of the DC/AC converter is now derived from this. The air above is important. The peak at the moment of switching on must be intercepted by the DC/AC converter. The exact power consumption of the TSC printer is not definitely clear, the 1200W converter seems to be at its limits. To get security, the 1800 W would be an alternative.
2. Workstation hours of operation
It's more about how long my battery lasts. A mixing ratio between usage time and standby time of the consumer is to be found as a basis.
The maximum power has already been calculated. The question of the average power consumption, i.e. normal operation, is therefore very important.
In normal operation we assume that the workstations consume around 30% of the power during operation. Please check the data sheet for this.
CAUTION: Does not correspond to the specifications for the standby mode.
In normal operation, the total power consumption is 1,230W * 30% = 369W, for example.
To put it simply, the power that is taken from the DC/AC converter must also be supplied.
AC side: Current draw: 369VA / 30V = approx. 1.6 A. This means that these 369VA must also be supplied on the 24V DC side.
DC side: power supply: 369 W / 24V = approx. 15 A
Thus, the current draw is about 15A from the battery. In this case, the power loss of the DC/AC converter is not taken into account.
If you now have a usage ratio of, for example, 50% in one shift (8 working hours). Need 15A per hour for four hours. So that's 60 Ah.
Latest technology - individually checked
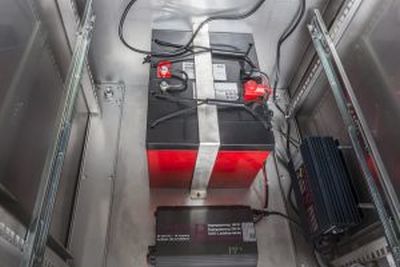
The batteries are manufactured using the latest technology and are individually tested. Thanks to a special manufacturing process, the AGM battery is extremely resilient and durable. This results in the high cycle stability. They are undoubtedly among the most robust and reliable maintenance-free AGM DEEP CYCLE batteries on the market
Properties ZL Deep Cycle.
- high cycle stability *see diagram
- maintenance-free
- locked
- leakproof
- long service life very low self-discharge
- Overpressure safety valve (VRLA technology)
Comparison of lead gel battery versus LiFePo
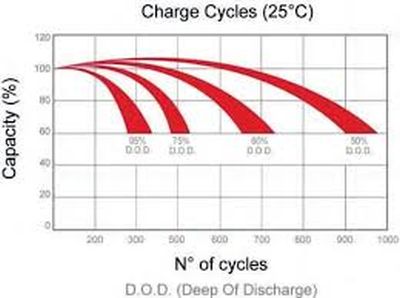
LiFePo4 battery technology is also increasingly being requested. Below is a list of benefits and a comparison:
- You only need about 50% of the lead capacity if you want to switch to LiFePo4, which results in weight and space savings of over 50%. li>
- 4 to 5 times the number of charging cycles results in a significantly longer service life.
- A full charge is not absolutely necessary with LFP.
- Very high charging efficiency, almost 100% of the energy fed in can be used again.
- Even 50Ah LFP can supply 1000W inverters at almost any charge level.
- High charging and discharging currents possible over the entire state of charge.
- A battery management system (BMS) is mandatory and already integrated.
- Flexible charging relaxation - lead chargers can also be used.
- Unlike LI-ION batteries, lithium batteries are intrinsically safe - there is no risk of fire.
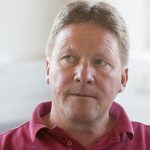
"Wir beantworten gerne Ihre Fragen."